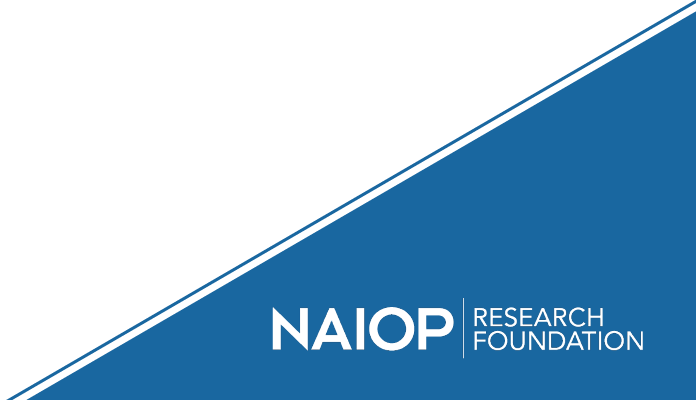
Reverse Logistics Strategies for the Post-pandemic Supply Chain: Spaces and Places to Recapture Value
Release Date: September 2024
Effective supply chain management is crucial for any organization operating in today’s complex business environment, and logistics is a key part of the supply chain equation. Given heightened competition, tightening margins and an increased focus on environmental sustainability, some consumer and industrial product companies are turning to reverse logistics (RL) as a “final frontier” where logistical competencies can generate financial success. RL involves the management of products and materials flowing backward in the supply chain from customers toward sources, after they have been returned or become obsolete. The aims of RL are to maximize the remaining value of returned items and minimize related costs.
Effective implementation of RL requires a carefully designed supply chain. Collaboration between commercial real estate practitioners and supply chain experts is essential to identify suitable locations for RL activities, negotiate favorable lease agreements and implement best-in-class facility designs. The NAIOP Research Foundation commissioned this report to provide insight into best practices in RL supply chain design and the implications for facility location and design. The study is of use to organizations seeking to improve their RL capabilities and to supply chain executives and developers interested in calibrating building design and location to maximize operational revenue and reduce costs. It specifies the types, characteristics and locations of facilities that businesses should incorporate into their RL networks. Appendix A at the end of this report provides a detailed description of the locational and design needs of RL facilities for specific industries. Key findings from the report include:
- Third parties that provide outsourced RL services generally need to be centrally located relative to the industry they serve, close to industry-preferred modes of transportation, close to the source of product returns, near a sufficiently large labor market, and have access to waste management infrastructure. They should seek to balance these locational priorities against real estate costs.
- For firms that insource RL, multiple smaller, regional facilities may in many cases be better than a single, centralized facility. Locational priorities (proximity to transportation, waste management infrastructure, labor and customers) are otherwise similar to those for third-party RL facilities, though their relative importance varies by industry.
- Real estate professionals can play a pivotal role in identifying suitable RL facility locations that meet supply chain managers’ strategic criteria.
- The decision to locate insourced RL processes in a dedicated facility or within a facility that also handles forward logistics depends on the firm’s industry and the scale of RL the facility must manage.
- A firm’s industry will also shape whether an RL facility should be built-to-suit or if a speculative project or existing facility can meet its needs. Either way, RL facilities require dedicated spaces for specialized tasks such as returns management, refurbishing, recycling, and waste management, and benefit from flexible interior design.
- Converting an existing warehouse or distribution center for RL usually does not require major changes to the building’s structure. However, RL facilities often require more power than traditional warehouses, and some need specialized docks, ramps and secure loading areas.